A manufacturing company with multiple production facilities faced challenges with equipment efficiency, maintenance costs, and production downtime. They engaged SateUp to implement an IoT solution that would monitor equipment performance in real-time and optimize production processes.
Proven Track Record
Customer Satisfaction
We Have Completed
Typically Responds Within
The Challenge
The manufacturing company operated seven production facilities across the country, running 24/7 operations with equipment ranging from legacy machinery dating back 15-20 years to newer automated systems. Despite their substantial capital investment in equipment, they were experiencing alarming inefficiencies that threatened their competitive position in the market. Unplanned downtime had increased by 37% year-over-year, with an average of 122 hours of production lost monthly across all facilities—translating to approximately $3.2 million in direct revenue loss annually. Each major equipment failure not only halted production but also triggered expensive emergency maintenance, rushed replacement parts, and overtime labor costs that were 3-4 times higher than planned maintenance expenses.
The company’s maintenance approach was predominantly reactive, with 78% of maintenance activities occurring after failures rather than before them. This reactive stance stemmed from a fundamental lack of visibility into equipment health and performance metrics. Maintenance teams relied on manual inspections and operator reports, which often came too late to prevent failures. The limited monitoring systems that were in place existed as isolated islands of automation, with no centralized way to aggregate or analyze data across different machine types, production lines, or facilities. Production managers had to compile reports manually from multiple systems, resulting in a 2-3 day lag in obtaining critical performance metrics—far too slow to enable proactive decision-making.
Energy consumption presented another significant challenge, with utility costs rising 18% over the previous two years. Without granular monitoring of energy usage by specific equipment and processes, the company struggled to identify optimization opportunities. Quality issues were also increasingly problematic, with defect rates hovering around 4.2%—well above the industry benchmark of 1.5%. The root causes of these quality problems were difficult to pinpoint without comprehensive data correlation between machine parameters and output quality. Additionally, the lack of standardized processes across facilities meant that best practices weren’t being shared, resulting in significant performance variations between locations doing identical work. The company’s leadership recognized that these interconnected challenges required a comprehensive solution rather than incremental improvements to individual systems.
SateUp Solution
We began with a comprehensive assessment of the client’s manufacturing ecosystem, conducting detailed audits of equipment, processes, and existing data infrastructure across all seven facilities. Our team collaborated closely with production managers, maintenance technicians, and C-suite executives to develop a phased implementation strategy that would deliver immediate value while building toward a comprehensive connected factory solution. Rather than a one-size-fits-all approach, we designed a flexible system architecture that could accommodate both legacy equipment and modern machinery.
At the core of our solution was a sophisticated IoT platform that transformed the client’s manufacturing operations from reactive to predictive. We deployed a network of over 1,200 industrial-grade sensors across critical equipment to capture vital parameters including vibration patterns, temperature variations, power consumption, pressure levels, and acoustic signatures. These sensors connected to edge computing devices that performed preliminary data processing and anomaly detection directly on the factory floor, enabling real-time alerts without reliance on cloud connectivity. The edge devices communicated with a central IoT hub that aggregated data across all facilities, creating a unified view of operations while maintaining data segregation for security and performance.
The platform’s advanced analytics engine was the transformative element that converted raw data into actionable intelligence. Using machine learning algorithms trained on historical failure data and normal operating patterns, the system developed equipment-specific health models that could predict potential failures up to 72 hours before they occurred. These predictive capabilities enabled the maintenance team to transition from reactive to condition-based maintenance, scheduling interventions during planned downtime and preventing catastrophic failures. We implemented digital twins for critical production lines, creating virtual replicas that enabled scenario testing and process optimization without disrupting actual production. The solution included customizable dashboards for different stakeholders—maintenance teams received real-time equipment alerts, production managers accessed efficiency metrics and bottleneck analyses, while executives gained insights into facility-wide performance indicators and improvement opportunities. The entire system integrated with the client’s existing ERP and MES systems, ensuring that IoT insights could directly influence production scheduling, inventory management, and resource allocation.
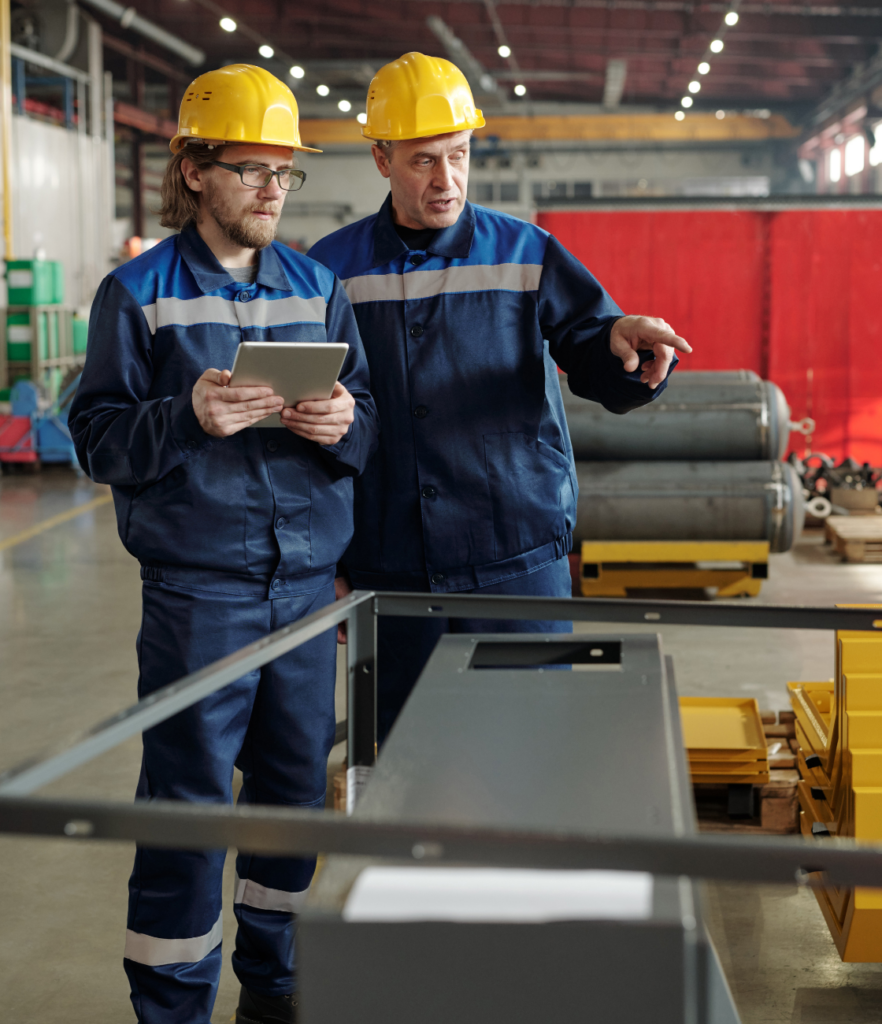
The Results
- 78% reduction in unexpected equipment downtime
- 42% decrease in maintenance costs
- 23% improvement in overall equipment effectiveness
- 35% increase in production throughput
- 19% reduction in energy consumption
- 68% improvement in predictive maintenance accuracy
- 3.2% increase in product quality metrics
- 27% reduction in spare parts inventory
- $4.7M in documented annual savings